In an industry-first, GKN Additive successfully adapts and enhances DP600 like material, a widely used low alloy dual-phase steel in the automotive industry, for AM manufacturing, and enables diverse designs and applications in Automotive and in other industrial sectors.
The newly developed metal powder materials DPLA (Dual Phase Low Alloy) and FSLA (Free Sintering Low Alloy) meet similar requirements for mechanical properties as DP600 (HCT600X/C), such as higher ultimate tensile strength (UTS) and low yield strength (YS) to UTS ratio, and can be used in Laser Powder Bed Fusion (DPLA) and Binder Jetting (FSLA) respectively - a true world first for these two additive manufacturing processes. The powder materials as well as parts manufactured with these materials are available for purchase immediately.
Target customers are the automotive industry - for example, to adapt the design of automotive sheet metal parts, or to develop completely new structural components - but also manufacturers in the industrial sector.
Capabilities of DPLA and FSLA go beyond the traditional automotive material DP600
It’s important to understand that DPLA and FSLA are more than the traditional automotive material DP600 (HCT600X/C) simply translated into AM. The new powder materials are specialized for additive manufacturing with regard to spreadability, laser absorption (Laser AM) and sinterability (Binder Jetting). As Christopher Schaak, Technology Manager for Binder Jetting at GKN Additive, explains: “Traditional DP600 offers specific standardized mechanical properties achieved by heat treatment.
The dual-phase steel AM materials developed by GKN Additive on the other hand are very flexible in their characteristics, as their mechanical properties can be tuned more widely by the heat treatment after the laser or binder jetting process.” This enables a variety of different use cases in the industrial sector as well and makes the material an interesting candidate for a wide spectrum of customers, as already shown in the IDAM project.
“By using a subsequent heat treatment process to achieve the desired properties with the material within a wide range (medium to high strength properties), an AM provider can use an established printing process that does not need to be changed”, says Sebastian Bluemer, Technology Manager Laser AM at GKN Additive. “This allows streamlining of internal processes and enables a faster product delivery.”
Before using DPLA and FSLA, GKN would first receive desired characteristics from a customer and then had to develop and qualify a new material for the laser powder bed fusion or binder jetting process to specifically meet these demands. This took significantly more time than the newly developed materials (DPLA/FSLA) with their predefined wide property field, where different mechanical characteristics can be achieved with one developed printing process, simply by varying the subsequent heat treatment.
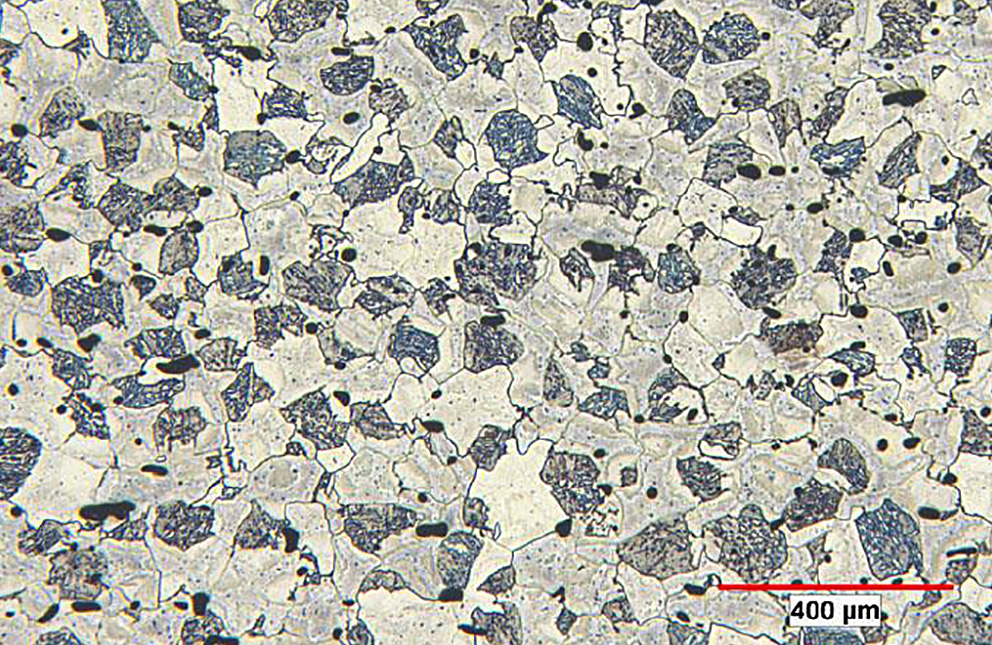
New design possibilities, faster functional validation, potential for weight reduction
For manufacturers in the automotive sector for example, these two materials offer a new level of design freedom and potential for weight reduction. “With these AM processes, manufacturers in the Automotive industry can construct body parts differently than what was possible with traditional sheet metal parts. If you look at a tailored blank, many sheet- metal parts and support parts need to be formed and joined together to achieve a certain stiffness. By using structural components printed with AM on the other hand, you would need less process steps and less material, leading to cost optimization and a weight reduction”, explains Christopher Schaak.
Furthermore, the time it takes for a new product to enter functional validation can be significantly shortened through AM processes. “Our customers want to know what the new AM material can achieve in their respective use cases,” says Sebastian Bluemer, “and how it can be used. It’s faster to print parts with AM than to retool complete traditional production lines and manufacture the parts the conventional way. This means that AM is a good solution to quickly and functionally validate a material and a component, and to analyze faster and more efficiently, whether the material can help with a specific application or not.”
Besides optimizing existing designs, both Binder Jetting and Laser Powder Bed Fusion with the new material can also be used to develop completely new designs (Design for Additive Manufacturing), for example bionic structures – which is where Additive Manufacturing truly shows its power.
Relevant Links:
Download the FSLA and DPLA Material Datasheet.
Join our Binder AM Business Case Challenge.
About GKN Additive
GKN Additive is a digital manufacturer of advanced AM parts and materials for prototypes, medium series, and the aftermarket, striving to push new technologies to the limit to make them simpler, faster and more accessible. GKN Additive is backed by GKN Powder Metallurgy’s expertise in powder production, metal processing and an engineering network of over 6,000 employees in 29 locations around the world.
Contact for journalists
GKN Additive
Susanne Trautmann, Global Marketing Manager
E-Mail: susanne.trautmann@gknpm.com